I. Overview:
The sensitivity of the fluorescent magnetic powder is mainly affected by the following three aspects: the peeling of the fluorescent powder, the magnetic saturation intensity and the contrast.
2. Peeling of phosphor powder:
The poor resistance to solvent immersion of the fluorescent magnetic powder leads to the peeling of the fluorescent powder from the fluorescent magnetic powder, which is the main factor affecting the sensitivity of the fluorescent magnetic powder. As shown in the figure below, the fluorescent magnetic powder produced by our company and the fluorescent magnetic powder purchased on the market are respectively dispersed in water, and then the fluorescent magnetic powder suspended in the solution is adsorbed to the bottom of the test tube with a magnet. We found that the fluorescent magnetic powder purchased on the market is prone to peeling, resulting in a large amount of fluorescent powder dissolved in the water; while the fluorescent magnetic powder of our company basically does not peel off, and the water is basically clear. The peeling of the phosphor powder reduces the phosphor powder on the magnetic powder, and the fluorescence brightness of the fluorescent magnetic powder decreases greatly, which leads to a decrease in the detection sensitivity; at the same time, the peeled phosphor powder is dissolved or suspended in the carrier liquid, which leads to an increase in the fluorescence brightness of the carrier liquid, and the fluorescence brightness of the inspection workpiece substrate. It will also increase, affecting the judgment of surface cracks, increasing the missed detection rate and reducing the sensitivity.
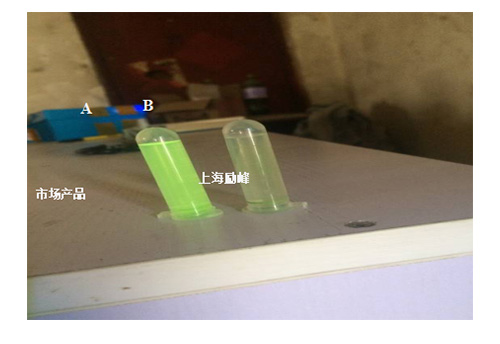
2. Magnetic saturation intensity:
Improper coating materials and processes lead to a significant decrease in the magnetic response of the magnetic powder (that is, the decrease in the magnetic saturation intensity), which is a secondary factor affecting the sensitivity of the fluorescent magnetic powder. The coating of organic matter will lead to the decrease of the magnetic saturation intensity of the inorganic magnetic powder, but the inappropriate coating material and process make the decrease of the magnetic saturation intensity more obvious. It can be seen from the figure below that the magnetic saturation intensity of the fluorescent magnetic powder purchased in the market is only about 40 emu/g, while the magnetic saturation intensity of the fluorescent magnetic powder produced by our company is about 100 emu/g. Controlling the magnetic saturation intensity of the coated fluorescent magnetic powder is an important guarantee for maintaining good flaw detection sensitivity.
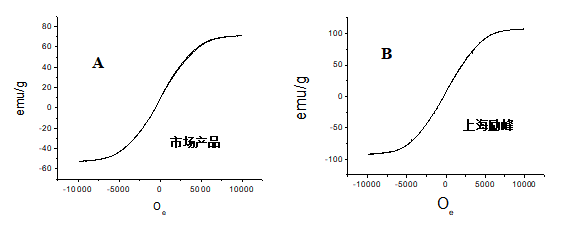
3. Contrast:
The so-called contrast in magnetic flaw detection is the difference between the fluorescence brightness of the magnetic trace area and the non-magnetic trace area. The greater the difference, the higher the contrast. The contrast is inversely proportional to the concentration of the magnetic suspension, that is, the higher the concentration of the magnetic suspension, the lower the contrast. The purpose of high contrast can be achieved by improving the suspension of the fluorescent magnetic powder and reducing the magnetic saturation intensity, but the sensitivity of the flaw detection process fluctuates. If the test block cannot be detected or the detection is not obvious), there will be missed detection. We believe that high contrast and high magnetic saturation are effective guarantees for high sensitivity in the entire flaw detection process. According to our observation, the concentration of fluorescent magnetic powder added in most flaw detection workers is too high, which will reduce the sensitivity of flaw detection, which also requires high-contrast fluorescent magnetic powder to ensure high flaw detection sensitivity. The high contrast ratio enables the fluorescent magnetic powder to be used in a wider range of concentrations during the flaw detection process, and the operability of the fluorescent magnetic powder is stronger in the flaw detection process. It can be seen from the figure below that the contrast ratio of our company's fluorescent magnetic powder is higher than that of the fluorescent magnetic powder on the market, and the same workpiece shows clearer cracks.
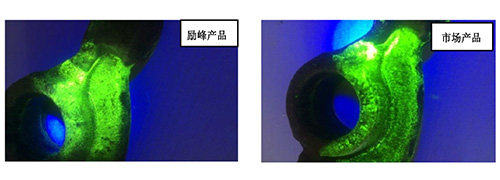