In order to make the workpiece easier to be magnetized, we require the demagnetizing field of the portable magnetic particle flaw detector to be small enough. So what determines the size of the demagnetizing field of the flaw detector?
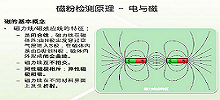
1. The size of the applied magnetic field determines the size of the demagnetizing field:
The stronger the applied magnetic field, the better the magnetization effect, the stronger the magnetic field generated by the equivalent N and S poles at both ends of the workpiece, and the stronger the demagnetization field outside the workpiece.
2. The size of the demagnetizing field is inversely proportional to the L/D value of the workpiece:
L refers to the total length of the workpiece, D refers to the maximum diameter of the section of the workpiece, and for a hollow cylindrical workpiece, D refers to its equivalent diameter, and its value is (the squared difference between the outer diameter and the inner diameter is taken as the square root); For hollow non-cylindrical workpieces, the D value is (the difference between the outer overall cross-sectional area and the inner hollow cross-sectional area is divided by π, and then multiplied by 2).
Under the same external conditions of L and D, the demagnetization field generated by the magnetized hollow workpiece is smaller than that of the solid workpiece; under the same D condition, the demagnetization field generated by the workpiece with longer magnetization length is smaller than that of the short workpiece.
3. The demagnetizing field is related to the geometry of the workpiece:
The demagnetization fields of workpieces with different geometries are different. Under the same magnetization, the demagnetization factors are different. For a complete closed ring specimen, N=0; for a spherical workpiece, N=0.333;
4. The demagnetization field is related to the form of magnetizing current:
When the magnetizing current adopts alternating current, the skin effect will be generated, and the penetration depth is shallower than that of direct current, and the N and S poles formed at both ends of the workpiece have poor magnetic properties.
The attention points of the flaw detector in terms of power-on and welding:
1. Power on:
(1) When using continuous magnetization, it is necessary to specify the power-on time to ensure that the magnetic powder can be used under power-on conditions;
(2) When using the remanent magnetization method, the magnetization time is generally 0.2-1s. When using the inrush current, it should be more than 10ms, and the power should be energized more than twice. If the magnetic particle flaw detector can have sufficient magnetic potential during flaw detection, then it is not necessary to follow the constraints of this regulation.
2. Welds
(1) One is that when heat treatment is performed on the weld after welding, flaw detection should be performed after the final hot working.
(2) For the flaw detection of hot-worked gaps and pressure vessels, the magnetization method should not use the method of direct current flow.